God.favored wrote:Got the car up and running again today, but it kept throwing the fan belt off and finally broke it. It was just an autozone belt that clearly was not the same style, but I remember my 63 having an automatic tensioner with a spring going to the back of the car on it and this car doesn't. does anyone know where I can get another one of these? I'll be ordering the correct belts from clarks tonight.


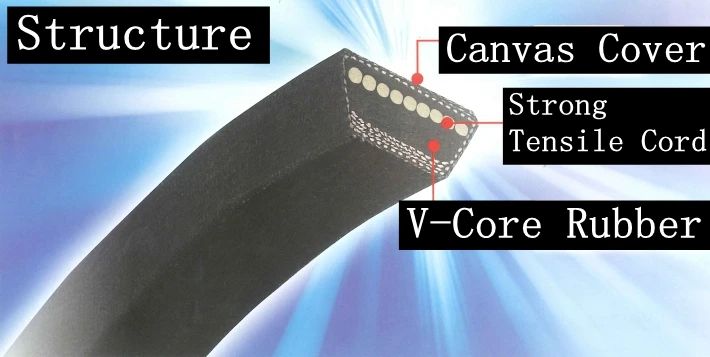


Note that the discussion above of the cause of internal belt fatigue refers to the normal stresses involved with a standard belt configuration in which the belt travels around pulleys that are all in one plane. Even a serpentine belt installation with a complex path follows pulleys that are all in a single alignment with each other, so the belts usually are not required to make a 90 degree turn — which is not the case with a Corvair belt layout — so the internal stresses on the Corvair belt are made even greater than the normal design expectation of belt design engineers by the unique Corvair drive belt that drives both a generator/alternator AND a cooling fan, AND makes a 90 degree turn in the process! The load-bearing fatigue factors in a Corvair installation are likely even greater than a normal vehicle installation because of the unique configuration in a Corvair engine. This would make the routine four-year replacement of the belt on a Corvair even more applicable in a Corvair application. The final comment about increased heat found in compact, modern engine compartments would also apply to the high ambient heat usually expected in the air-cooled Corvair engine compartment.Motor Drive Belts
On today's vehicles, it's very difficult to tell the difference between the automotive drive belt with 50,000 miles of wear, and another belt with 10,000 miles of wear. A basic change in engine belt construction – one that produced a longer-lasting belt – also makes it difficult to spot indications of belt wear.
Virtually all automotive drive belts produced in the U.S. and Europe are made without a cover. These "bandless" belts don't show wear like their predecessors. Although bandless belts are designed to outlast banded belts on similar drives they provide no early warning of failure.
There are two main causes of drive belt failure. The most common is fatigue of the load-bearing, tensile cords leading to belt failure from the inside out. Tensile cord failure is due to a gradual weakening of the tensile cords that results from the combination of side stress, bending stress, and centrifugal force imposed on the belt as it travels around the pulleys.
Because this type of failure takes place inside the belt, there is no easy way to determine when the belt is about to break. Statistics show that the chance of drive belt failure on an average vehicle goes up sharply after four years.
For this reason, many drive belt manufacturers recommend that all engine drive belts be replaced on a four-year basis.
The other major cause of drive belt failure is improper tension. This causes the belt to slip as it travels around the pulleys, generating heat build-up. Excessive heat eventually causes the rubber compounds in the belt to break down, and crack, leading to belt failure.
Indicators of belt tension problems include:In addition, small engine compartments on today's vehicles make belts more susceptible to heat and contamination from petroleum products. High temperatures can cause belts to dry, harden and crack. If a belt becomes oil-soaked, it cannot grip the pulley. Petroleum products also break down the rubber compounds in the belt. The best way to check belt tension is with a tension gauge. Because of smaller engine compartments and shorter belt spans between pulleys, the old finger deflection method of checking tension is not as accurate. http://arrc.ebscohost.com/ebsco_static/ ... _BELTS.htm
- Belt squeal, especially on the fan or power steering drives.
- Battery discharge sometimes caused by a slipping alternator belt.
- Excessive sidewall wear that allows the belt to ride lower than normal in the pulley grooves.
- Absences of overcord (the belt's top protective covering).
- Excessive cracking, or rib chunking (pieces of the ribs breaking off).
I am not convinced of the value of the various automatic tensioners that have been marketed for Corvairs. One of the greatest advances made by engineers on the Corvair for increasing belt longevity was the switch to the lightweight magnesium cooling fan that was introduced in 1964. Prior to that year the cooling fans used on the Corvair were much heavier steel construction. This heavy fan design acted like a flywheel. In the normal course of driving engine speeds vary frequently – especially when shifting years – and the heavy cooling fan would resist changes in crankshaft pulley speed. The fan belt would have to endure the stresses as the crankshaft pulley changing rotational speed and the cooling fan continually resisting those changes. The introduction of the lightweight magnesium cooling fan greatly reduced fan belt stress.

